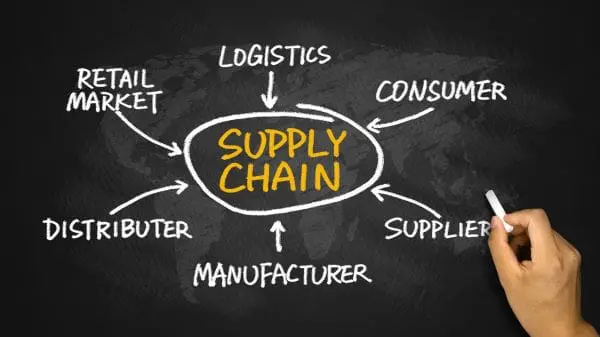
A supply chain disruption can impact your ability to serve customers and run a profitable business. Issues can creep up at any time too. While you may not be able to prevent these disruptions entirely, you can take steps now to minimize their impact and be prepared, so your business operations recover faster.
On this page, we’ll cover a few types of supply chain disruptions, explore real-world examples, and then cover some tips that will help your business be more resilient.
What is a Supply Chain Disruption and Why Does it Happen?
A supply chain is comprised of all entities involved in creating a product and delivering it to a customer. It starts with the raw goods and finishes when the end user receives it.
For example, let’s say you decide to purchase a gold ring online. The first link in the supply chain is the raw materials, or the gold used to create the ring. The company mining probably sells the gold to a supplier. A manufacturer then takes it and turns it into a ring. The online retailer buys it, then sells it to you and ships it off.
Five entities are involved in this very basic example. There’s usually more than one type of raw good involved and often more links in the supply chain. If any of those links face an issue that prevents that ring from being made or reaching you, it’s considered a supply chain disruption.
Types of Supply Chain Disruptions
There are lots of supply chain disruption examples in everyday life. A few are covered below.
- Pandemics: Supply chain disruptions from COVID-19 impacted 94 percent of Fortune 1000 companies, per Accenture research. Although this is an extreme example, it happens more often than people think. For example, the Swine Flu and the Avian Flu caused similar issues.
- Natural Disasters: Hurricanes, floods, fires, earthquakes, and other natural disasters can cause supply chain issues too. For example, the 2011 Great Tohoku Earthquake and Tsunami took out a power plant in Japan. Because the plant-powered a factory that made components used in 60 percent of vehicles, carmakers across the globe were forced to shut down for a period of time. Wildfires across the western United States cause similar chaos by creating a shortage of wood used for pallets.
- Transportation Delays: Issues like the trucker shortage, inclement weather, and seasonality often cause supply chain disruptions too.
- Price Fluctuations: Cost shifts can happen for a variety of reasons. For example, when fires impact wood availability for pallets, the cost to make them naturally rises. Some manufacturers have reported costs doubling almost overnight. As trucking companies have had to work harder to keep pros behind the wheel, transportation costs go up too. Most people became acutely aware of pricing fluctuations during the pandemic as well. The price of eggs, for example, skyrocketed by more than 30 percent. The cost of PPE, such as masks and gloves that medical professionals rely on, has risen exponentially.
- Cyber Attacks: Sometimes hackers specifically target a company, such as when Colonial Pipeline was hit with a ransomware attack. The incident disrupted gas supplies and increased prices. Other times, the attack is broader. The SolarWinds hack is an example of this. Often referred to as one of the biggest cybersecurity breaches of the 21st century, the hackers involved exploited a vulnerability in Orion software created by SolarWinds and used by more than 30,000 organizations to manage their IT. Once the malicious code was installed on an Orion system, it could spread to the data and networks of the business’s customers and partners. In other words, it effortlessly spread across entire supply chains, including government agencies.
How to Prepare for Possible Supply Chain Disruptions
Disruptions can happen at any time, so it’s important for businesses to take a proactive approach to supply chain risk management. Supply chain risk management commonly emphasizes the process of mitigation, reflecting limitations, additional tasks, and audits that adversely impact the value, as well as the complexity and velocity of sourcing processes and operations.
Strengthen Your Supplier Relationships
If you have strong relationships with suppliers, they’ll do their best to look out for you when there are supply chain disruptions. Treat suppliers like they’re part of your team, communicate with them often, and always pay them on time.
Build Up Your Inventory
Try to keep enough inventory on hand so that you have some breathing room and time to pivot if you face supply shortages. Remember that tying up working capital in excess inventory can hinder business growth. Identify the sweet spot for your business that allows you to run lean without compromising your ability to fulfill orders or meet demand if there’s an issue.
Supply Chain Planning System
Supply chain planning systems typically include the following components: Sales and operations planning offer businesses the opportunity to make better decisions that are informed by key supply chain drivers, such as sales, production, inventory, and marketing. By adopting the tenets of modern supply chain planning systems and relying on data instead of predictions, businesses can help make their operations and supply chain more agile and resilient.
Have a Customer Demand Management Strategy
There may come a time when you need to shift how you’re operating. It’s best to think through potential solutions when you’re not under pressure and are more likely to catch any unintended consequences of your intended path.
GM’s issues in the wake of the Japanese earthquake and tsunami are a prime example here. The company’s supply chain is massive and highly organized. Each component of a vehicle can take weeks or more to produce and needs to arrive on the assembly line at just the right time, as explained by MIT.
The company became unable to produce heated seats because of supply chain disruptions related to its electronic control modules. As a result, some company insiders called for GM to stop ordering the seats, but Bill Hurles, executive director of Global Supply Chain, recognized that path would have unintended consequences.
A shift away from heated seats would necessitate a shift away from leather seats, which heaters are commonly paired with. The company would then need to increase fabric seat orders, which could create its own set of issues. Furthermore, the lack of leather seats would impact the packages typically offered in vehicles, as higher-end models usually come with leather. Lastly, the company would still have leather seats and heated seats in various stages of preparedness scattered throughout its supply chain. Resolving the problem would be complicated.
GM decided to stay the course. Despite the fact that moving away from heated seats seemed like an easy solution, it created far more problems than it solved.
Explore various ways your business can manage customer demand if you’re in a similar situation, such as:
- Substitution: Find ways to guide consumers to a product that isn’t impacted by the current supply chain issue, such as increasing the price of the affected item and lowering the price of a substitute item that isn’t.
- Dilution or Stretching: See if there are ways to make your raw goods go further without impacting the quality and upsetting customers.
- Triage: Know which products will receive priority treatment if you’re forced to decide which to produce or whom to serve.
- Auction: Some companies switch to selling their products to whoever is willing to pay the most. Although this strategy can provide an immediate payout, it can also alienate loyal customers and damage the business in the long run.
Identify Backup Suppliers and Diversify Your Supplier Base
Work with a few different suppliers that come from different backgrounds. That way, if a regional or individual issue impacts one, you can bump up your orders with the others. Continue working with them and building up your relationships, so they’re more likely to help you out if you’re facing an issue.
Conduct a Supply Chain Vulnerability Audit
A key component of supply chain risk management is pinpointing potential issues in an audit or vulnerability assessment. This involves jotting down all of your raw materials and components, then making note of what controls or protections are in place for each. Then, use a four-point scale (very high, high, low, negligible) to assess the vulnerability of each item.
When you know your biggest risks, develop a plan to minimize the risk or establish a backup plan to ensure you won’t be without the item if there are delays or shortages.
How to Deal with a Supply Chain Disruption
Although you can take steps to minimize the impact of a supply chain disruption, it’s not always possible to prevent issues altogether. However, these tips can help you bounce back quicker.
Plan for Recovery
Keep the long-term health of your business in mind as you navigate supply chain issues. How you handle the disruption will impact how your customers and suppliers feel about you afterward.
Communicate with Customers
At a bare minimum, customers who are already waiting on delivery need to know why it’s delayed, what you’re doing to address the issue, and when you anticipate a resolution. However, it’s better if you set the right expectations by communicating before someone places an order. Consider sending an email to your loyal clients or including information on your website.
Evaluate the Impact on Cash Flow
Supply chain disruptions can:
Identify how the supply chain disruption impacts your cash flow and be prepared with a backup source of funding that can help you cover expenses if needed while you’re working things out.
Assess Buyer Behavior
Demand for certain products and services may shift while you’re working through your supply chain issues. Keep a pulse on what your customers want to see if there are opportunities to pivot away from products or services that have become difficult to produce.
Boost Cash Flow During Supply Chain Disruptions with Invoice Factoring
Invoice factoring is often used by companies that are experiencing rapid growth because it provides debt-free funding by accelerating payment on B2B invoices. However, it’s also an excellent option as a backup source of working capital because it’s flexible. When you factor and which invoices you factor is up to you. Plus, factoring can be tapped into quickly whenever the need arises, with the option to receive your advance as soon as the same day you submit your invoice. To learn more or get started, request a complimentary rate quote from Charter Capital.
- How Factoring Supports Business Continuity Plans - March 17, 2025
- Factoring vs. Supply Chain Financing: Which is Right for You? - February 17, 2025
- 10 Essential Financial Skills for Business Leaders - January 20, 2025